Understanding the Metal Fabrication Process: Insights from Los Angeles Experts
Introduction to Metal Fabrication
Metal fabrication is a crucial process in the manufacturing industry, involving the creation of metal structures by cutting, bending, and assembling. This process is essential for producing a wide range of products, from small components to large-scale industrial machinery. In Los Angeles, metal fabrication experts offer insights into the sophisticated techniques and technologies that drive this industry.
Understanding the intricacies of metal fabrication can be beneficial for those interested in manufacturing or engineering. By exploring the various stages and methods involved, one can gain a comprehensive view of how raw materials are transformed into functional metal products.
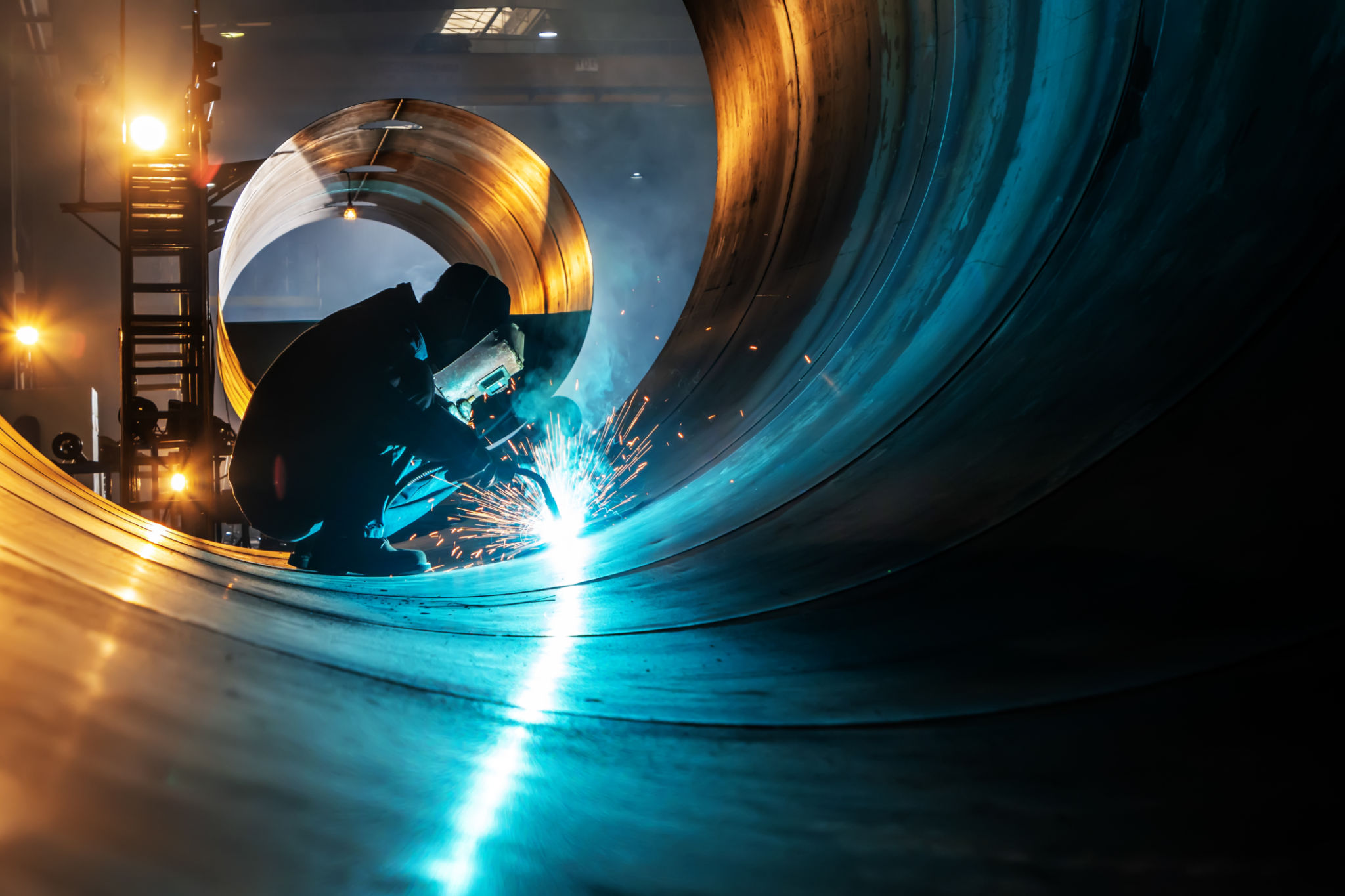
The Metal Fabrication Process
Cutting and Shaping
The first step in metal fabrication is cutting, where raw metal sheets are resized into desired shapes. This can be done using various methods such as shearing, laser cutting, or water jet cutting. Each technique offers unique benefits; for example, laser cutting provides precision and speed, making it a popular choice among fabricators.
Once cutting is complete, the next step involves shaping the metal. This is typically achieved through bending or rolling, which helps form the metal into the required shape. These processes require skilled technicians who understand the material properties and can manipulate them without causing damage.

Joining and Assembly
After shaping, the metal parts are ready for joining. This phase involves welding, riveting, or using adhesives to assemble the components into a final product. Welding is one of the most common methods due to its strength and durability. Los Angeles experts emphasize the importance of quality welding to ensure the longevity and safety of the finished product.
Assembly requires precision and attention to detail. Each piece must align perfectly to ensure the product functions as intended. This stage often involves rigorous quality checks to ensure all components fit correctly and meet industry standards.

Technological Advances in Metal Fabrication
Automation and Robotics
The metal fabrication industry has seen significant advancements with the integration of automation and robotics. These technologies have revolutionized how metal parts are fabricated, offering increased efficiency and precision. Automated systems reduce human error and allow for faster production cycles, which is especially beneficial in large-scale operations.
Robotics also play a vital role in repetitive tasks such as welding and material handling. By utilizing robots, companies can maintain high-quality standards while enhancing worker safety by minimizing exposure to hazardous environments.
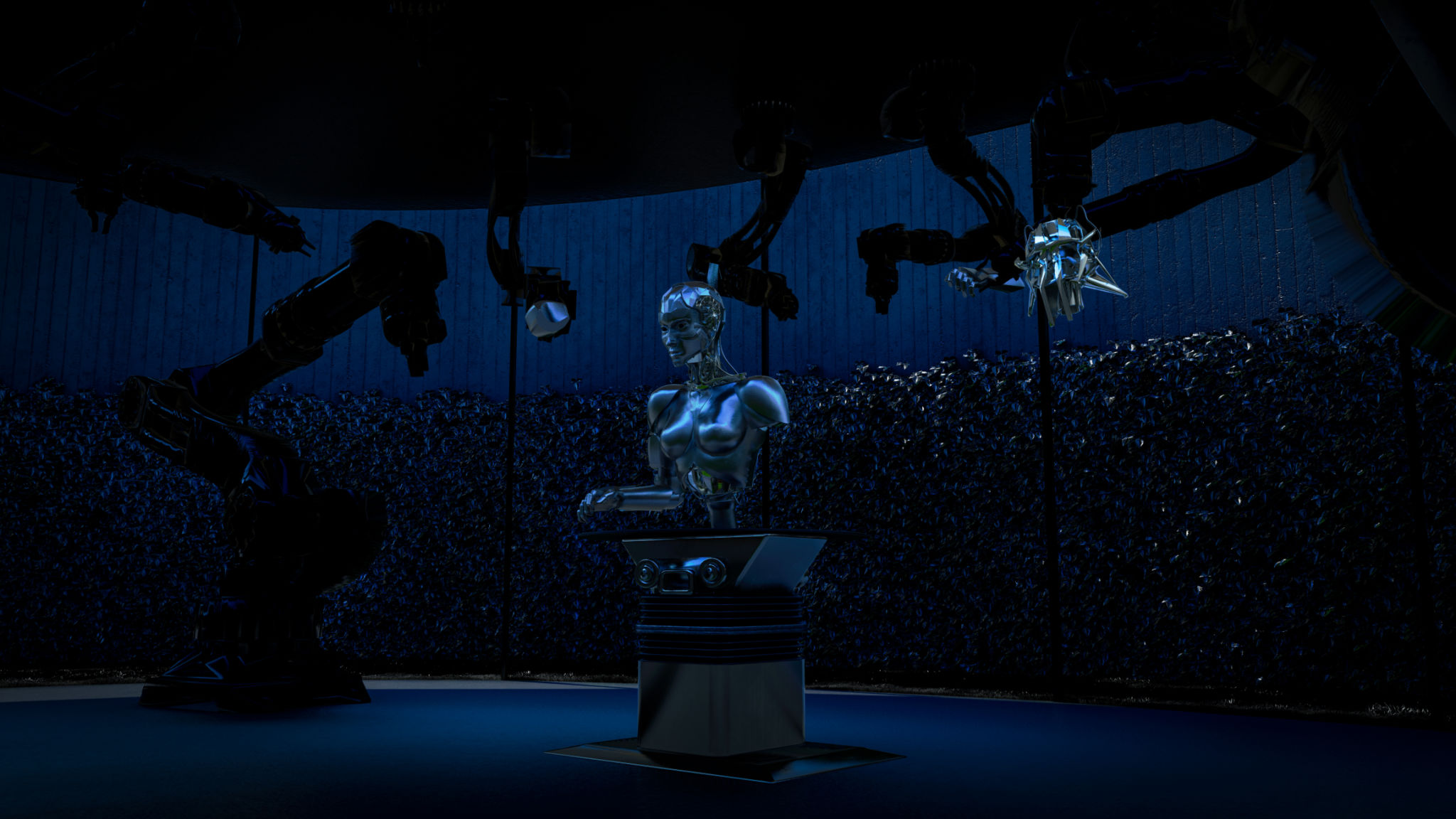
Computer-Aided Design (CAD)
Another technological leap in metal fabrication is the use of Computer-Aided Design (CAD) software. CAD allows engineers to create detailed 3D models of products before fabrication begins. This technology enables precise planning and reduces the likelihood of errors during production.
With CAD, fabricators can simulate different scenarios to optimize the design and identify potential issues early in the process. This not only saves time but also reduces material waste, making the process more cost-effective and environmentally friendly.
Conclusion: The Future of Metal Fabrication
The metal fabrication industry continues to evolve with advancements in technology and methodology. In Los Angeles, experts are at the forefront of these changes, constantly adapting to new tools and techniques to enhance productivity and quality.
As we look to the future, it's clear that innovation will remain a key driver in metal fabrication. By embracing new technologies and processes, the industry will continue to meet the growing demands for high-quality metal products across various sectors.